When it comes to additive manufacturing, Fused Deposition Modeling (FDM) has gained significant popularity due to its cost-effectiveness and versatility. However, understanding the intricacies of FDM cost is crucial for businesses looking to leverage this technology. In this article, we will delve into the various factors that contribute to the Fused Deposition Modeling Cost and what industry professionals should consider in this regard.
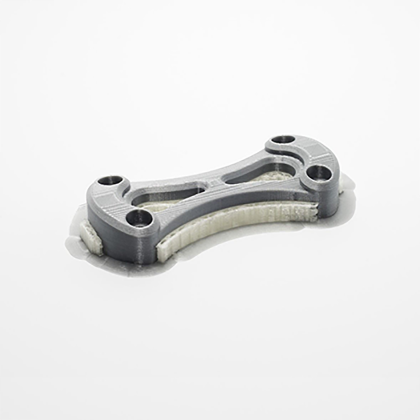
Material Costs
One of the primary components of Fused Deposition Modeling Cost is the material used for 3D printing. The type and quality of the filament can significantly impact the overall cost. High-performance materials such as ABS, PLA, or PETG may come at a higher price point compared to standard thermoplastics. Additionally, specialty filaments with unique properties, such as flexibility or conductivity, can further elevate the material costs.
Equipment and Maintenance
Investing in FDM printers and ensuring their proper maintenance is another crucial consideration for businesses. The initial capital outlay for acquiring 3D printers, along with ongoing maintenance and repair costs, should be factored into the overall Fused Deposition Modeling Cost. Moreover, the energy consumption of the equipment and the need for periodic upgrades or replacements should not be overlooked.
Labor and Time
While FDM offers automation in the printing process, labor costs are still relevant, especially in post-processing activities such as support removal, surface finishing, and assembly. Additionally, the time taken to complete a 3D printing job directly influences the overall cost. Factors such as printing speed, layer height, and complexity of the design can impact the production time and, subsequently, the labor costs involved.
Quality and Waste Management
Ensuring the quality of 3D printed parts is essential, but it can also contribute to the Fused Deposition Modeling Cost. Higher quality standards may necessitate additional processes such as calibration, testing, and inspection, all of which add to the overall expenses. Moreover, managing material waste, especially in cases of failed prints or support structures, requires careful consideration to minimize costs and maximize efficiency.
As we have explored the various components that make up the fused deposition modeling cost, it becomes evident that a comprehensive understanding of these factors is imperative for businesses to make informed decisions. By carefully analyzing material costs, equipment investments, labor requirements, and quality considerations, industry professionals can effectively manage the overall cost of FDM and optimize their additive manufacturing operations.